Installation Guide
Bending parts should be used in installations where the expansion will be bidirectional and in runs exceeding 5 meters in length. Expansion loops cannot be removed for direction change, an expansion chamber must be designed. The shape of this expansion loop is given below.
To determine the minimum width of an expansion chamber, the following calculations should be performed:
In situations where a change in direction cannot compensate for linear expansion, the installation of an expansion loop may be required. The minimum pipe bend, Amin, can be calculated using the following formula, taking into account a safety margin of 150mm to accommodate for potential increases in elongation due to temperature fluctuations:
The length of the freely moving part can then be calculated using the following formula:
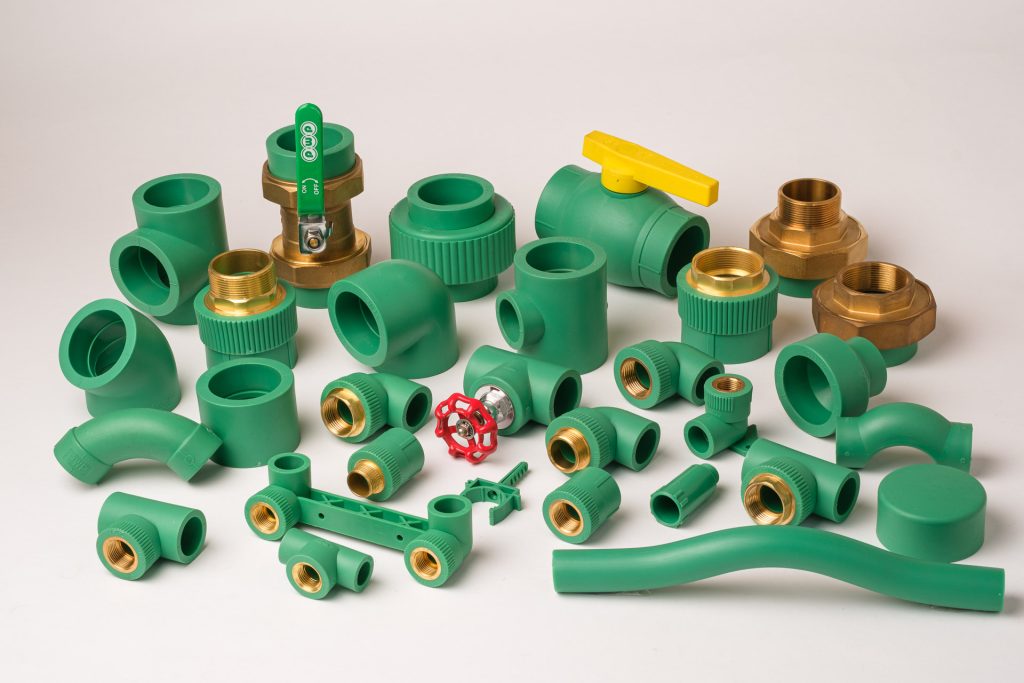
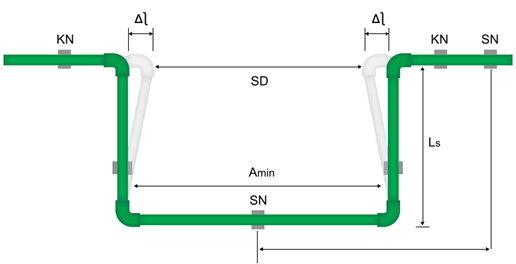
Amin = 2 x ∆ ∫ x SD
Amin: Minimum width of expansion loop
SD: Safety margin (150mm)
Ls: Length of freely moving part (mm)
D: Pipe outer diameter
∆ ∫: Amount of elongation (mm)
L: Pipe length (m)
K: Specific constant of material (K=30)
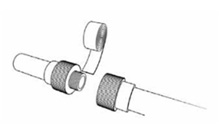
For screw-type joints, threaded fittings must be used. Cutting thread directly to plastic components is not permitted. Threads are sealed with a special Teflon tape or sealing compounds.
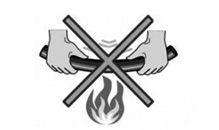
Components must not be subjected to open fire.
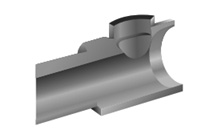
Polyfusion welding or electric and butt welding techniques are used to join plastic parts. The result is a high-quality homogeneous joint. A correct working process and appropriate tools must be used in joining procedures. Welding PWP components together with other brands is not suggested (because of warranty issues)
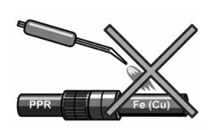
If the pipeline continues with metal piping beyond a combined pipe fitting, then no welding or brazing is allowed near this point due to possible hazard of heat transfer to the fitting.
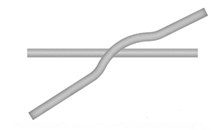
Pipeline crossings are made by using components which are specially designed for this purpose.
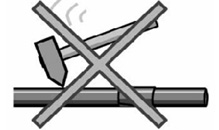
Components of PWP piping systems must be protected against falling, impact, blows or another mechanical damage during transport and installation.
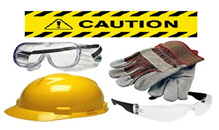
Wear protective equipments.
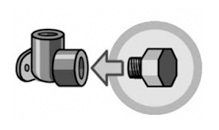
To cap off a pipe, e.g. if elbows for wall mounting or wall assemblies are to be closed before mounting outlet fittings, an end cap is used (for example during pressure tests, etc.)
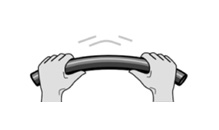
Pipe bending should be done at +15°C. The minimum bending radius for pipes of diameter range 16 – 32 mm is eight diameters. (preferable not to)
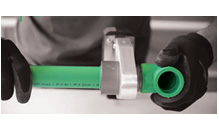
Pipes and fittings are joined by termofusion at 260ºC, with appropriate welding equipment provided by PWP. Connect to power (220V) and wait until the green control light switches off. From that moment on, you can start working.
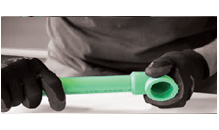
Simultaneously, warm up the entire depth of the pipe and the end of the fitting with the poly welder, applying slight pressure. Once the heating period has finished, join the pieces without interruptions.
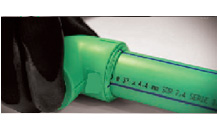
During a short period of time, you may readjust the welded parts (do not rotate over 30º).
A few minutes later, the fusion will reach its maximum strength.
For small holes in the pipe, such as holes from nails or screws, you can use the repair pin shown here. For larger holes, install and cap a fusion outlet fitting or remove the pipe and fuse in a new section.
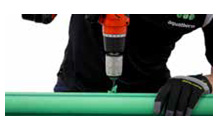
If the hole is too small, carefully drill it out.
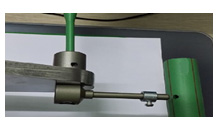
Insert the repair head into the pipe, and insert the repair pin into the repair head. Heat for 5 sec.
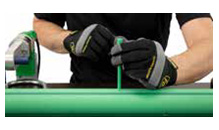
Remove the pin from the iron head and the repair head from the pipe. Insert the pin into the pipe wall. Do not over-insert the pin.
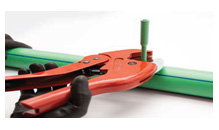
Cut off protruding end of the repair stick; The repaired area of the pipe has reached full strength after approximately 5 minutes.